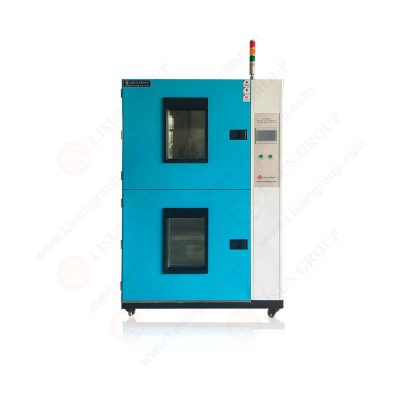
The high and low temperature shock test chamber is the necessary testing equipment for metal, plastic, rubber, electronics and other material industries. It is used to test the material structure or composite material. Detect the chemical change or physical damage of the sample caused by thermal expansion and contraction in the shortest time.
The high and low temperature shock test is used to assess the adaptability of the product to the sharp change of the ambient temperature. It is an indispensable test in the identification test of the equipment design and the routine test in the batch production stage. In some cases, it can also be used for environmental stress. screening test. It can be said that the frequency of application of the thermal shock test chamber in verifying and improving the environmental adaptability of equipment is second only to vibration and high and low temperature tests.
The high and low temperature shock test chamber is divided into three-chamber type and two-chamber type according to the test requirements and test standards. The difference lies in the test method and internal structure.
The three-chamber type is divided into a cold storage room, a heat storage room and a test room, and the product is placed in the test room during testing. The two-chamber type is divided into a high-temperature room and a low-temperature room.
The high and low temperature switching is realized through the movement of the basket driven by the motor. The product is placed in the basket and moves with the basket.
Working principle of refrigeration:
Both the high and low refrigeration cycles adopt the reverse Carroll cycle, which consists of two isothermal processes and two adiabatic processes.
The process is as follows: the refrigerant is adiabatically compressed to a higher pressure by the compressor, which consumes work to increase the exhaust temperature, and then the refrigerant conducts heat exchange with the surrounding medium isothermally through the condenser, and transfers the heat to the surrounding medium.
Finally, the refrigerant expands adiabatically through the valve to do work, and the temperature of the refrigerant decreases at this time.
Finally, the refrigerant absorbs heat isothermally from the object with higher temperature through the evaporator, so that the temperature of the object to be cooled is lowered. This cycle is repeated so as to achieve the purpose of cooling.
In fact, as a tool, the high and low temperature impact test chamber has different purposes in different stages of product development:
1. The engineering development stage can be used to find product design and process defects;
2. Provide basis for product finalization or design identification and acceptance decision in batch production stage;
3. When used as an environmental stress screening application, the purpose is to eliminate early failures of products.
Rapid change of temperature difference in High and Low Temperature Thermal Shock Chamber:
1. The product has beautiful appearance, reasonable structure, advanced technology, excellent material selection, easy operation and reliable equipment performance.
2. Double-chamber hanging basket structure, the upper high-temperature chamber, the lower low-temperature box, the impact method is the high-temperature chamber, the low-temperature chamber stops, and the test piece is quickly moved into the high-temperature chamber by hanging and moving up and down to achieve cold and hot impact test.
3. The metering device adopted, the controller adopts a large-scale man-machine dialogue man-machine interface controller, Chinese and English LCD screens, and various complex programs can be set. The program setting adopts man-machine dialogue, which is easy to operate, easy to learn, stable and reliable.
4. Adopting advanced circulating air design, the indoor temperature is uniform and avoids any dead angle; the perfect safety protection device avoids any potential safety hazards and ensures the long-term reliability of the equipment.
Test requirements:
initial temperature requirements
Although the general thermal shock test standard does not mention or do not make rigid regulations on the starting temperature of the thermal shock test, this is a problem that must be considered when the test is carried out, because it involves whether the test ends at low temperature or high temperature State, which determines whether the product needs to be dried, resulting in extended test time.
If the test is completed and the low temperature standard test product is taken out of the High and Low Temperature Thermal Shock Chamber, it should be recovered under normal test atmospheric conditions until the sample reaches a stable temperature. This operation will inevitably cause condensation on the surface of the test sample. The effect of dew introduction temperature on the product. thereby changing the nature of the experiment.
Test time requirements:
1. Stipulates the lower limit of 1h, that is, the temperature stabilization time is less than 1h, it must be 1h; if it is greater than 1h, use the time greater than 1h;
2. There are 5 time levels from 10min to 3h given in GB2423.22. According to the temperature stabilization time of the product measured by the thermal shock test chamber, the time closest to it or the optional time level is used, and the closest time is directly used. A similar time is used as the hold time;
3. In 810F method 503.4, no specific time or optional time level is specified, and the time when the product reaches temperature stabilization or the actual exposure time of the product in the environment is directly used.
The performance indicators of the High and Low Temperature Thermal Shock Chamber are as follows:
The accuracy is reflected by the difference between the set value and the actual detection value. The popular point is the uniformity and volatility of the chamber.
The “mid-test test” uses high and low temperature resistant circulating fans in the high temperature area and low temperature area. Circulation, no matter how uniform the temperature is, it will not exceed ±3°C, and the fluctuation of the chamber is ±0.5°C (when the shock stabilizes and returns to the constant temperature in the stable chamber).
The functional technical indicators of the High and Low Temperature Thermal Shock Chamber include impact sensitivity, temperature conversion speed, and accuracy.
In the temperature shock test, the most critical thing is to establish the stress caused by the inconsistent thermal expansion and contraction of different materials.
The actual thermal shock is most likely to occur on the outside of the product under test. Relevant data point out that it is not necessary to stabilize the temperature of the entire product, but as long as the surface and temperature of the product under test are consistent with the test temperature.
High and Low Temperature Thermal Shock Chamber can be used in the temperature shock test and fast-changing temperature test in a wide range such as aviation, air space, electronic components and material research.
HLST-500D has two separate chambers: high temperature chamber and low temperature chamber.
HLST-500T has three separate chambers: high temperature chamber, low temperature chamber and test chamber.
HLST 500D High and Low Temperature Thermal Shock Chamber
https://www.lisungroup.com/news/technology-news/the-role-of-high-and-low-temperature-shock-test-chambers-in-material-and-component-testing.html
Comments
Post a Comment