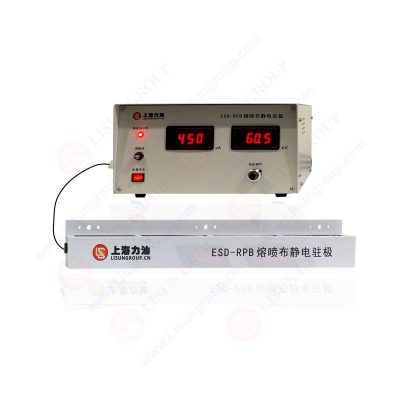
In 2020, a global outbreak of the pandemic resulted in a shortage of protective equipment such as masks, primarily due to the scarcity of one of the main raw materials, melt-blown fabric. As a consequence of the melt-blown fabric shortage, some individuals began attempting to produce their own, leading to varying qualities of melt-blown fabric products in the market.
Against the backdrop of intensified government crackdowns on counterfeit products, electrostatic flocking equipment for melt-blown fabric has become an indispensable auxiliary product for melt-blown fabric production. Consequently, a range of meltblown electrostatic flocking equipment has emerged in the market, with prices ranging from thousands to tens of thousands of dollars.
For customers, understanding the principles behind electrostatic flocking equipment for melt-blown fabric is crucial when selecting the appropriate equipment. Electrostatic flocking equipment employs the principle of static electricity to generate static electricity on the surface of melt-blown fabric, causing the fibers of the fabric to quickly stretch and form a fine fiber network under the action of static electricity, thus facilitating the production of melt-blown fabric.
Therefore, customers should consider factors such as the electrostatic generation effect, stability, service life, and ease of operation when selecting electrostatic flocking equipment for melt-blown fabric. Furthermore, it is advisable to purchase products from reputable manufacturers to avoid purchasing counterfeit products and ensure that the produced melt-blown fabric meets the required quality standards for protective equipment production.
The three key process parameters affecting the effectiveness of electrostatic flocking are polarization time, polarization voltage, and polarization distance. As the polarization time increases, the equivalent surface charge density deposited will increase, leading to a higher potential on the surface of the flocking material. With further increases in polarization time, when the surface potential of the filtering material is sufficiently high, charges below the needle tip will be repelled and moved to areas with lower charge density. When polarization ends, the charge surface density reaches saturation. Therefore, further increases in polarization time will not significantly change the filtering efficiency of the material.
ESD-RPB Particulate filtration efficiency tester
Electrostatic flocking equipment plays a crucial role in mask production lines. Also known as electrostatic generators, these devices are specifically designed to generate static electricity, with stable output voltage, comprehensive protection, and simple operation. They offer advantages such as high efficiency, low resistance, antibacterial properties, and energy-saving features. During the mask production process, electrostatic flocking equipment sustains the production of high-voltage static electricity, primarily to impart static electricity to the non-woven fabric melt-blown fabric, ensuring that the mask achieves a filtration efficiency of not less than 95% for aerosols containing Staphylococcus aureus with a diameter of (3±0.3) μm.
These devices employ dedicated high-voltage power supplies and digital control methods, with features like full abnormal slow start and nanosecond arc response capabilities, ensuring continuous and stable operation of the melt-blown fabric production line, free from faults, and capable of operating around the clock. Additionally, their small energy storage and nanosecond arc response capabilities ensure rapid restart within 20 milliseconds, ensuring uniform and stable electrostatic effects. Consequently, the high stability of electrostatic flocking equipment makes it an indispensable key equipment in mask production lines.
The Meltblown Fabric Electrostatic Charging Generator from Shanghai LISUN possesses the following characteristics:
• High safety performance, with comprehensive protection functions.
• Excellent electrical performance, with good moisture resistance, no leakage, stable performance, and high precision.
Capable of imparting static electricity to mask raw materials, ensuring that the filtration efficiency of the mask for aerosols containing Staphylococcus aureus with a diameter of (3±0.3) μm reaches not less than 95%.
• Utilizes a dedicated high-voltage power supply and digital control method, with full abnormal slow start and nanosecond arc response capabilities, ensuring continuous stable operation of the melt-blown fabric production line, fault-free operation, and uninterrupted operation.
• Small energy storage, ensuring no harm to non-woven fabric during discharge and ignition; nanosecond arc response capability ensures rapid restart within 20 milliseconds, ensuring uniform and stable electrostatic effects, with high stability.
• Possesses advantages such as high efficiency, low resistance, antibacterial properties, and energy-saving features, enhancing electrostatic adsorption and improving filtration efficiency on the basis of the physical collision barrier effect of conventional filter materials.
https://www.lisungroup.com/news/technology-news/principle-and-technical-features-of-meltblown-fabric-electrostatic-charging-generator.html
Comments
Post a Comment