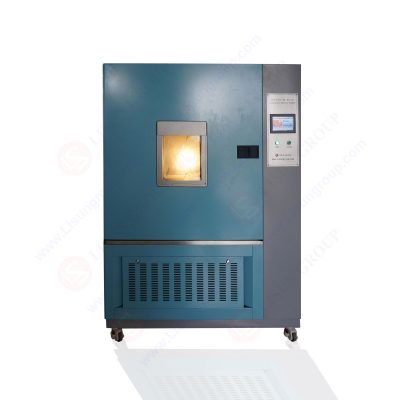
The high and low temperature test chamber is an essential device for conducting reliability tests on industrial products. It simulates high and low temperature environments to examine the performance indicators of various products, including electronic appliances, automotive components, aerospace equipment, and marine weaponry.
The principle behind the operation of the high and low temperature test chamber primarily relies on temperature control and regulation. Let’s first delve into high-temperature control. Heating is a crucial step in achieving high temperatures within the chamber, which is relatively straightforward. Typically, the chamber employs far-infrared nickel-chromium alloy high-speed heating wires for heating purposes. Temperature control is achieved through a P·I·D+S·S·R system to ensure precise and efficient energy utilization.
For low-temperature operation, increasing the number of heating wires and enhancing the temperature control software’s performance are necessary for rapid heating and achieving high temperatures. Additionally, the refrigeration system plays a pivotal role in achieving low temperatures. The chamber’s refrigeration system typically comprises a fully enclosed compressor unit produced by a French company, utilizing fluorine refrigerants for cooling. Its operation principle is based on the reversed Carnot cycle, compressing the refrigerant to a higher pressure through the compressor and then exchanging heat with the surrounding medium through the condenser to achieve cooling.
In summary, the high and low temperature test chamber achieves the transition between high and low temperatures through the synergistic action of temperature balance and control systems. In continuous operation, the control system utilizes PID automatic calculation to adjust the output of the heater, ultimately achieving dynamic balance and ensuring the stable operation of the chamber.
Standard Operating Procedures for High and Low Temperature Test Chamber:
• Power Connection: Start by connecting the user’s power source and switching on the power switch, usually located on the side panel of the control cabinet.
• Standby Check: Allow the chamber to run for at least 60 seconds and check for any phase sequence alarms.
• Cooling Water System: Activate the cooling water pump’s power switch and open the inlet and outlet valves for the cooling water. Ensure that the drain valve is closed before opening. Monitor the water pressure gauge readings at the inlet and outlet, ensuring the pressure is between 0.2~0.6Mpa with a pressure difference greater than 0.2Mpa. Additionally, ensure the water temperature does not exceed 28℃.
• Humidification Device Setup: If humidity operation is required, turn on the power switch for the humidification device and the water pipe valve.
• Setting Test Parameters: Set the required temperature and humidity parameters on the temperature chamber’s control panel.
• Start the Test Chamber: After setting the test parameters, start the test chamber and enable the over-temperature protection.
• Fault Handling: In case of any alarms during the test, refer to the “Installation and Maintenance Manual” for troubleshooting procedures and address the alarm accordingly.
GDJS-015B Temperature Humidity Chamber | Thermal Chamber
Common Dehumidification Methods for High and Low Temperature Test Chamber:
1. Refrigeration Dehumidification Method:
The refrigeration dehumidification method condenses the water vapor in the air on the cold surface, forming water or frost. During the test process, when the air’s water vapor comes into contact with the cold surface, it condenses into water or frost, which is then removed from the test chamber. However, prolonged testing may cause frost buildup on the cold surface, affecting the dehumidification efficiency. Therefore, it is essential to control the cold surface temperature above 0℃ to prevent frost buildup.
2. Solid Desiccant Dehumidification Method:
The solid desiccant dehumidification method absorbs water vapor from the air to achieve dehumidification. This method is typically used for tests requiring lower dew point temperatures, such as around -70℃. Solid desiccants have a lower surface water vapor pressure, enabling them to achieve lower humidity requirements. However, this method is relatively inconvenient to use and may require specialized equipment, so it is generally only used when the test has specific requirements.
In some special test scenarios, such as testing internal combustion engines at low temperatures or during operation, a large amount of air needs to be supplied for fuel combustion. To prevent excessive frost buildup on the evaporator of the low-temperature chamber due to the water vapor in the new air, a solid desiccant-based rotary dehumidifier that can operate continuously is typically used for dehumidification purposes.
https://www.lisungroup.com/news/technology-news/unveiling-the-working-principle-and-operational-procedures-of-high-and-low-temperature-test-chamber.html
Comments
Post a Comment