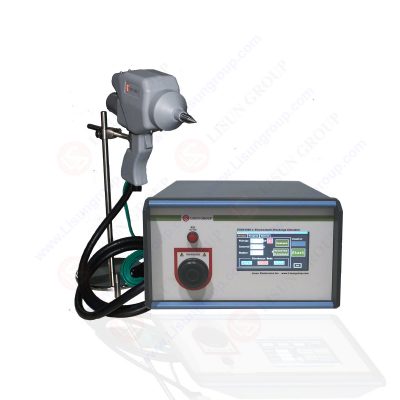
What is Electrostatic Discharge (ESD)?
Electrostatic Discharge (ESD) is one of the common sources of interference in electronic devices. According to the national standard GB/T17626.2 (equivalent to the international standard IEC61000-4-2), Electrostatic Discharge (ESD) Immunity TestingESD immunity testing is an essential step to ensure devices are protected from the disruptive effects of electrostatic discharge. ESD occurs naturally and is often observed when humans come into contact with semiconductor devices. For instance, as people walk on synthetic fiber carpets, friction between shoes and the carpet can cause the accumulation of electric charges on the body, leading to electrostatic discharge. Such discharge can generate voltages of up to 15kV, with current pulse waveforms having rise times between 100ps to 30ns.
Why Conduct Electrostatic Discharge Testing?
Electronic engineers have found that electrostatic discharge can potentially cause semiconductor materials to break down, resulting in irreparable damage to devices. Additionally, electrostatic discharge and subsequent changes in electromagnetic fields can pose risks to the normal operation of electronic equipment. Through electrostatic discharge immunity testing, the resistance of devices to electrostatic discharge can be assessed, ensuring their reliability and stability in practical usage.
The primary purposes of electrostatic discharge testing include:
Assessing device resistance to electrostatic discharge: By simulating scenarios where humans interact with devices while charged, electrostatic discharge testing determines whether devices can effectively withstand external electrostatic discharge interference.
Testing device stability and reliability: Through testing, the performance of devices under electrostatic discharge interference is evaluated to ascertain their stability and reliability in real-world usage.
The electrostatic discharge testing process typically involves the following steps:
• Setting test conditions: Parameters such as humidity and temperature are set according to standard requirements.
• Simulating human body charging: Specific friction methods are used to induce electric charges on the human body, ensuring compliance with testing requirements.
• Device contact testing: The charged human body is brought into contact with the device under test, and any electrostatic discharge occurrences and their potential impacts are observed and recorded.
• Result evaluation: Test results are evaluated to assess the device’s electrostatic discharge resistance and determine compliance with standard requirements.
Through electrostatic discharge immunity testing, potential issues devices may face when exposed to electrostatic discharge can be identified early, allowing for appropriate measures to be taken to enhance device stability and reliability.
The Electrostatic Discharge (ESD) immunity test simulates two scenarios:
• Direct discharge: When personnel directly touch the device, causing discharge, and its impact on the device’s operation.
• Indirect discharge: When personnel touch nearby equipment, affecting the test device.
The consequences of electrostatic discharge include:
Direct discharge can lead to damage to semiconductor components in the device, resulting in permanent failure.
Discharges (whether direct or indirect) can cause changes in the near-field electromagnetic field, potentially leading to unintended operation of the device.
ESD61000-2_Electrostatic Discharge Simulator
Discharge methods include:
• Direct discharge: Contact discharge is the preferred form, only using air-gap discharge when contact discharge is not feasible, such as when there are insulating layers on surfaces or gaps in computer keyboards.
• Indirect discharge: This includes horizontal coupling (HCP) and vertical coupling (VCP).
The Electrostatic Discharge (ESD) immunity testing evaluates the device’s resistance to electrostatic discharge by simulating these discharge methods and scenarios, analyzing potential impacts to ensure device reliability and stability during actual use. The preference for contact discharge as the primary discharge method stems from shortcomings revealed during the implementation of the precursor to the IEC61000-4-2 standard, the IEC801-2 standard. The IEC801-2 standard exclusively used air-gap discharge, but issues regarding repeatability and comparability arose during its implementation.
The primary reasons for these issues include various constraints on the discharge current waveform of air-gap discharge, such as the speed at which discharge electrodes approach the device under test, the influence of the device’s surface shape on the distribution of electric field strength, environmental factors (such as temperature, humidity, and air pressure), and the effect of discharge voltage on the current waveform spectrum. Additionally, at the time, measurement instruments were inadequate to meet requirements, such as oscilloscopes lacking the bandwidth to observe waveforms with rise times as fast as 1 ns.
To address the shortcomings of air-gap discharge on test results, corrections were made in the 1991 draft of the IEC801-2 standard, deciding to prioritize contact discharge. However, air-gap discharge was still retained for testing devices with non-conductive surfaces (such as plastic enclosures or metal casings covered with insulating materials). This decision persisted until the issuance of the IEC61000-4-2 standard.
Experimental content of electrostatic discharge testing includes:
• Clarifying the typical operating state of the device under test, including its functions, performance, and operating modes.
• Determining whether the device under test is tested as a benchtop device or a floor-standing device to ensure that the testing process reflects actual working conditions.
• Identifying the locations for applying static electricity, including critical parts and interface positions of the device under test.
• Specifying whether contact discharge or air-gap discharge is used at each application site to simulate possible electrostatic discharge scenarios in actual working environments.
• Determining the level (1 to 4, and optional open levels) to test the product based on requirements from the client or manufacturer.
• In conformity testing, specifying the number of discharges at each application site to ensure the accuracy and reliability of the test results.
Results of electrostatic discharge immunity testing should be classified based on the loss of functionality or performance degradation of the device under test. The relevant performance levels are determined by the device manufacturer, test requester, or mutually agreed upon by the manufacturer and purchaser of the product.
It is recommended to classify as follows:
A Level: Performance is normal within the limits specified by the manufacturer, test requester, or purchaser.
B Level: Temporary loss or reduction of functionality or performance, but can self-recover after the disturbance stops without requiring operator intervention.
C Level: Temporary loss or reduction of functionality or performance, requiring operator intervention for recovery.
D Level: Permanent loss of functionality or performance degradation due to hardware or software damage, or data loss.
The classification is determined based on the actual situation of the device and the requirements of the manufacturer to ensure an accurate assessment of the device’s resistance to electrostatic discharge.
https://www.lisungroup.com/news/technology-news/the-purpose-and-operational-procedure-of-electrostatic-discharge-esd-immunity-testing.html
Comments
Post a Comment