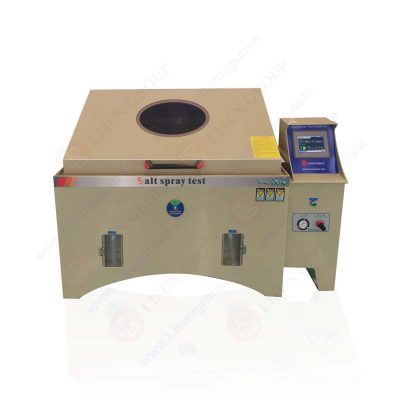
The Impact of Salt Spray on Electronic Products and Mitigation Measures
Salt spray is widely present in marine, atmospheric, terrestrial, lake, and river environments, inevitably exposing electrical and electronic products to salt-laden atmospheres. The effects of salt spray environment, ranking just after temperature, vibration, humidity, and dust, significantly accelerate the electrochemical corrosion process of metals, leading to the following issues:
Corrosion damage to components and fasteners
• Mechanical parts and components seizing or malfunctioning
• Circuitry opening or short-circuiting
• The Importance of Salt Spray Testing
To evaluate the corrosion resistance of products in salt spray environments, salt spray testing has become a necessary method. By simulating salt spray conditions, salt spray testing reveals the product’s ability to withstand corrosion, helping manufacturers improve product design and material selection to enhance reliability and longevity.
The corrosion damage to electronic products in salt spray environments can be mainly attributed to two factors:
• Conductivity of salt solution: Salt solution is conductive, triggering and accelerating electrochemical corrosion.
Increased resistance due to salt spray corrosion products: Corrosion products increase resistance, leading to resistance increment and voltage drop, thereby affecting the electrical performance of the product, causing performance degradation and losses.
• Salt Spray Test: Understanding its Impact on Electronic Products and Countermeasures
Salt spray testing is an effective method for evaluating the corrosion resistance of metal materials and their coatings. Common salt spray tests include the following three types:
• Neutral Salt Spray Test (NSS):
Widely used to evaluate the corrosion resistance of metal materials and their metallic or inorganic non-metallic coatings.
• Acetic Acid Salt Spray Test (AASS):
Mainly used to test the corrosion resistance of metal coatings and not suitable for organic coatings.
• Copper Accelerated Acetic Acid Salt Spray Test (CASS):
Similar to the acetic acid salt spray test, primarily used to test the corrosion resistance of metal coatings, but accelerates the corrosion process by introducing copper ions.
Salt spray testing is used to assess a product’s resistance to salt spray corrosion. Test results reflect the condition of surface damage, such as:
• Blisters
• Rust
• Decrease in adhesion
• Spread of corrosion at scratch sites
YWX/Q-010_Salt Spray Test Machine
Comprehensive evaluation standards for salt spray test results are not yet widespread, but they are recommended in the following national standards:
• GB/T 1766-2008 Rating Methods for Aging of Paint and Varnishes
• GB/T 6461-2002 Rating of Samples and Specimens on Metal Substrates and Other Inorganic Coatings After Corrosion Tests
Types and Mechanisms of Salt Spray Corrosion
Salt spray corrosion is a common electrochemical corrosion phenomenon that primarily affects metal materials and electronic products. Its corrosion mechanisms involve anodic activation and cathodic reactions. Here are different types of corrosion and their mechanisms:
Surface Corrosion
• Pitting Corrosion: Localized corrosion that forms holes or pits deeper than wide on metal surfaces.
• General Corrosion: Uniform removal of material from the surface, resulting in large areas of material loss.
Pitting Corrosion
Pitting corrosion selectively attacks specific points on metal surfaces, forming holes or pits deeper than wide. It’s often difficult to detect but can cause significant damage to materials.
Crevice Corrosion
Occurs in narrow crevices where differences in concentration of the corrosive medium create potential differences, exacerbating corrosion at poorly ventilated areas like around bolts and gaskets.
Dealloying
Selective dissolution corrosion, common in materials like brass, where zinc is dissolved, leaving behind a porous copper structure. Similar processes occur with denickeling and dealuminizing.
Rust
Formation of iron oxide and hydroxide corrosion products on iron and steel surfaces, causing loss of shine and gradual corrosion.
Salt spray corrosion occurs electrochemically, with the main mechanisms being:
• Anodic reaction: Metal atoms leave the lattice, oxidizing at the anode and releasing electrons.
• Cathodic reaction: Chloride ions dissociate at the cathode, reacting with metal ions and hydroxide ions to form corrosion products.
The three elements necessary for corrosion are water, oxygen, and ions. While coatings can delay corrosion to some extent, when the salt concentration in water exceeds 0.4 mol/L, sodium and chloride ions can penetrate coatings, leading to metal corrosion. The specific corrosion ability depends on the metal’s electrode potential sequence and the acidity or alkalinity of the environment.
To mitigate salt spray corrosion, common protective measures include:
• Surface coatings: Applying corrosion-resistant coatings such as galvanizing, nickel plating, etc., to prevent contact between the corrosive medium and the metal surface.
• Structural design optimization: Reducing gaps and contact areas between metal parts, adding sealing structures to prevent salt spray ingress.
• Material selection: Choosing materials with excellent corrosion resistance, such as stainless steel and special alloys.
Conclusion
Salt spray corrosion significantly affects metal materials and electronic products. Understanding different types of corrosion and their mechanisms is crucial for developing effective protective measures. By applying corrosion-resistant coatings, optimizing structural design, and selecting corrosion-resistant materials, the ability of products to withstand salt spray environments can be significantly improved, ensuring long-term reliable operation.
https://www.lisungroup.com/news/technology-news/understanding-salt-spray-testing-a-key-technology-for-evaluating-the-corrosion-resistance-of-metals-and-electronics.html
Comments
Post a Comment